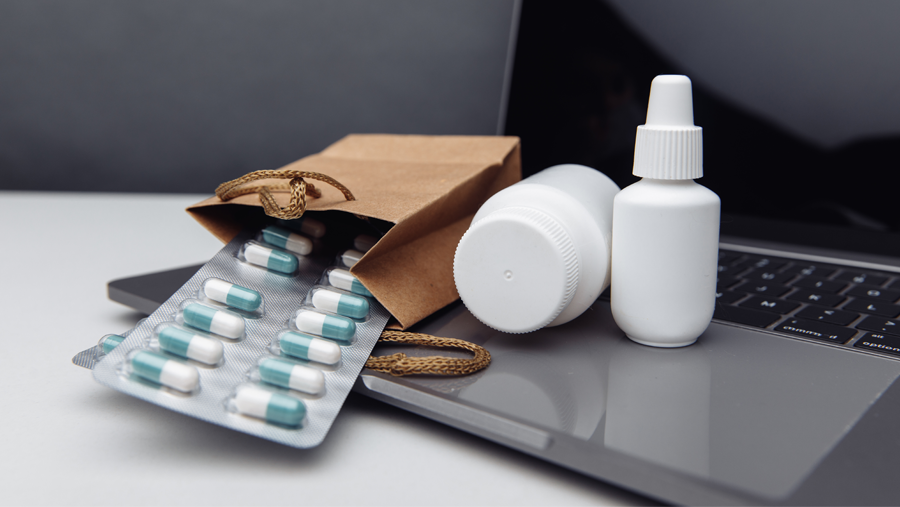
Pharmaceutical products are potent, essential products that need to be safeguarded during packaging, storage, and transportation to preserve and maintain their efficiency throughout their shelf life and reaching their end user. So, when it comes to the efficient packaging solutions that can be used for this, pharma desiccants have emerged as the best suitable option that provides sustainable, affordable, and durable packaging for pharma products. Pharma desiccants play a crucial role in preventing damage to pharmaceutical products during shipping and delays, especially in crises that can see unexpected delays or cancellations. These highly efficient moisture-absorbing materials, such as silica gel, molecular sieve, and clay, are used in the packaging of pharmaceutical products to protect them from moisture, which can cause physical and chemical changes, compromising the pharmaceutical product's quality and safety.
What is the Importance of maintaining pharmaceutical product quality?
Ensure product quality & safety - A pharmaceutical company’s goal is to make the medication that works. The products have been made to save the life instead of causing harm. The pharmaceutical industry and every employee of Pack Time are involved in pharmaceutical quality assurances, maintaining focus on the people taking the medications and the potential impact on their health.
Avoid negative publicity – The robust pharmaceutical quality assurance system ensures that products are effective and safe. Following good manufacturing practices (GMP) and enacting comprehensive inspection policies help the manufacturers produce the highest assurance and protect against negative publicity.
Improve efficiency – Pack Time’s pharmaceutical quality assurance is primarily about producing reliable and safe products. The second aspect of pharma quality assurance is that it promotes continuous improvement from technology transfer to product development.
Types of desiccants in Pharma
Now there are types of desiccants in pharma which have been listed below:
Montmorillonite Clay – Montmorillonite clay is a naturally absorbent that is created by the controlled dying of magnesium aluminum silicate of the sub-bentonite type. This clay is successfully regenerated for repeated uses at a very low temperature without substantial swelling. However, this property causes the clay to give up moisture readily into the container as the temperature rises.
Silica Gel – Silica gel is silicon dioxide it is a naturally occurring mineral that is purified and processed into either beaded form. Silica gel performs best at room temperature and high humidity and will drop the relative humidity in a container down to around 40%RH. As with clay, silica gel, with its wide range of pore sizes, has the capability of absorbing compounds other than water. The relative order of absorbability is water, ammonia, alcohols, aromatics, diolefins, olefins, and paraffins. When the potential for multicomponent adsorption is present, expect the more strongly adsorbed compounds, such as water, to displace the more weakly held ones.
Calcium Oxide - Calcium oxide is calcinated lime having a moisture absorptive capacity not less than 28.5% by weight. The distinguishing feature of calcium oxide is that it will adsorb a much greater amount of water vapor at a very low relative humidity than other materials. It is most effective where a low critical relative humidity is necessary, and where there is a high concentration of water vapor present. Calcium oxide removes water from a package very slowly, often taking days to reach its maximum capacity. As the calcium oxide absorbs moisture, it swells. Proper desiccant packaging is required for effective use.
Calcium Sulphate – Also known as the drierite T is created by the controlled dehydration of gypsum. It is a general-purpose desiccant geared mainly towards laboratory use. It is chemically stable, non-disintegrating, nontoxic, and non-corrosive, and does not release its absorbed water easily when exposed to higher ambient temperatures.
Overview of detrimental effects
Drugs approved by the US Food and Drug Administration for sale in the United States must be safe and effective on the benefits of the drug must be greater than the known risks. However, both the prescription and the over-the-counter drugs have side effects.
Defining the point side effect is also known as the adverse reaction, an unwanted undesirable effect that is possibly related to a drug. Side effects can vary from minor problems like a runny nose to life-threatening events such as a heart attack and liver damage.
If you are worried about any of your medicines, seek immediate medical attention. Active ingredients in medicines can ‘clash.’ So, taking more than one medicine at the same time can increase the risk of side effects.
Tell your doctor about all the medicines you are taking. You may like to have an annual review of all your medications.
Preservation of stability and shelf life
Pharmaceutical stability testing is one of the important factors determining factors such as a product’s shelf life, optimal storage conditions, retest period, and assuring its overall quality for consumers. Now during the stability test, manufacturers observe their products for any change in the physical, chemical, biological, and microbiological makeup of the substance. The stability testing guidelines are set by the International Council of Harmonisation of the Technical Requirements for Pharmaceuticals for Human Use.
Ensure product quality and compliance
- Pharmaceutical companies follow strict guidelines to comply with all applicable regulations and produce quality products.
- The Pharmaceutical company must work with many moving parts to ensure that product quality and manufacturing processes are safe.
- Pharmaceutical Companies must have their quality management systems in place to comply with all regulations.
- Quality management system continuously monitors all aspects of the manufacturing process from the production of the raw material to the final product.
- Pharmaceutical Companies must also have a quality control system to help them spot potential problems and find ways to fix them before they cause them to become product defects.
- Pharmaceutical Companies must constantly test their products to ensure they are still meeting high-quality standards. Testing allows companies to identify potential problems early on so that they do not result in sub-standard products getting to the market.
Common challenges faced by the Pharmaceutical Industry
- Reduced R&D investments – Currently many Pharmaceutical companies have reduced their investment in launching their new pharmaceutical products. High failure rates, high drug development costs, and low returns on investment discourage the pharmaceutical industry from product development.
- Consumer attitudes – Some consumers distrust medications and are willing to try more alternative therapies.
- Drug affordability – Many medications are not affordable for patients due to their income, the price of the drug or even the health insurance coverage.
- Government and insurance company policies – Due to the government regulations after effect drug regulations which can make new treatment launches cumbersome whereas the insurance companies decide who is the payer and set the reimbursement standards.
Conclusion
Desiccant packaging includes its effectiveness in preventing mold, mildew, and corrosion. Moreover, it enhances product stability during storage and transportation, contributing to overall customer satisfaction and reducing potential returns or complaints. Desiccant packaging is environmentally friendly, as many desiccants are reusable or can be disposed of safely. It also aids in preserving the integrity of sensitive items like electronics and pharmaceuticals. As a cost-effective solution, desiccant packaging provides a reliable method for industries to protect their goods and maintain quality standards.